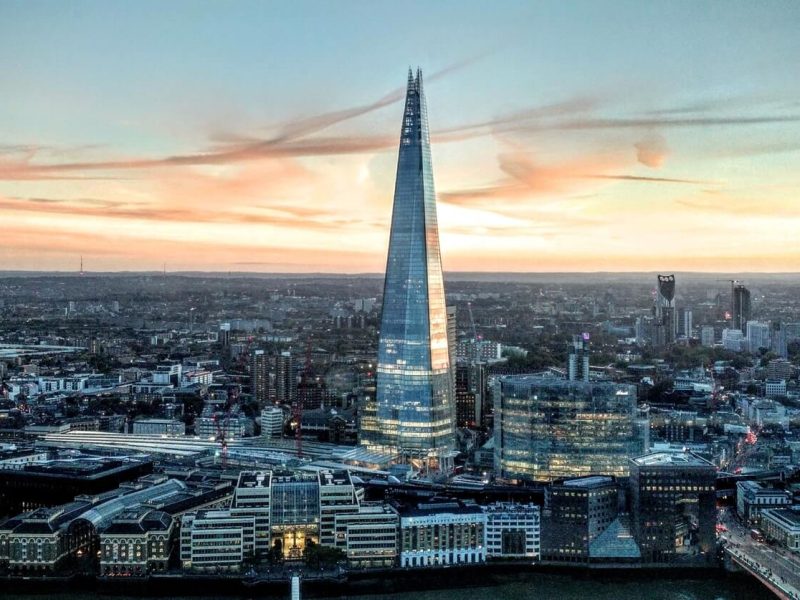
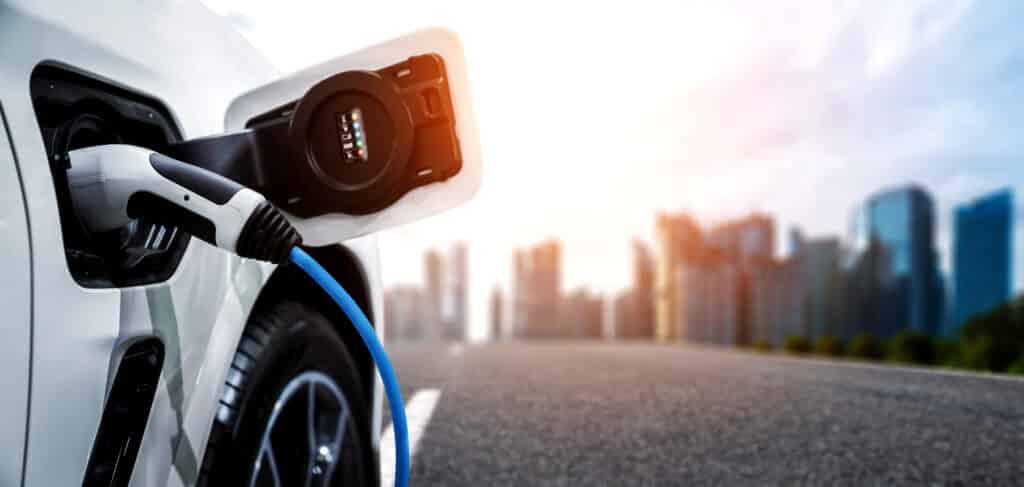
What drives EV forward?
The automobile industry is experiencing a major shift, with most automakers saying that the next ten years will be more transformative than the preceding two decades. Everything from materials and gasoline to pricing and business models to bring about more significant change in just the next few years, prompting wide-scale adoption of electric vehicles (EVs). The adoption of a cleaner and more efficient mode of transport is as much about governmental policies and the recognition to strive for greater efficiency as it is about cutting-edge breakthroughs in the automotive technologies.
Government subsidies and policies
Early adoption of electric light-duty vehicles (LDVs) was supported by significant tax advantages, which spurred the growth of the EV manufacturing and battery industries. The programs, which included purchase subsidies and/or car purchase and registration tax rebates, were designed to bridge the price gap between electric and conventional vehicles.
Subsidies for EVs are usually thought of as a one-time measure. Regardless, many nations presently provide subsidies to EV customers, with subsidies accounting for almost half of all EV purchases. Subsidies may be gradually phased out as EV technology lowers prices substantially. This phase-out might be complemented by levies on traditional cars to compensate for the negative externalities associated with their emissions.
Environmental concerns
Because transportation is the leading cause of climate change and a major source of other pollutants that harm human health, electrifying our cars is hailed as a critical measure.
The adoption of EVs has become increasingly important in reaching fuel economy and CO2 emissions targets. The largest set by the European Union had a significant impact on electric car sales making up 18.0% of total car registrations in 2021, up from a 10.5% in 2020, the fastest annual growth rate ever. As a solution to the detrimental effects caused by pollution from Internal Combustion Engine (ICE) vehicles, some governments have established sales objectives for electric vehicles that must be met. California’s zero-emission vehicle (ZEV) policy was initially implemented in 1990, prompting a faster transition to EVs which made up 10% of new car sales there in 2021.
The combustion engine has been a roaring success for the past century but we are already turning into the corner of something much better, something much simpler that will continue to provide us with the mobility we have become accustomed to but in a cleaner, lighter, and more sensible fashion- electric vehicles.
Main components of today’s EV
The modern EV is beyond being a concept and the primary components can be easily identified as the following:
Battery
The battery serves as a power source and is the most expensive part of the EV. The electricity that is stored in the battery is used to power the electric motor, which turns the wheels, whisper-quiet and with zero emissions. Due to the high expense of replacement, electric car batteries must last as long as possible, unlike portable devices, which fail after a few years.
The battery capacity determines how far your car can drive. The greater the capacity, the greater the distance traveled. Increasing the vehicle’s range by adding extra batteries is not the best solution. It raises the weight and limits the available space needlessly. As a result, fuel economy and energy efficiency suffer. Using smaller and more energy-efficient batteries is the greatest method to increase driving distance.
Battery Charger/Onboard charger
EVs get their battery charge from the grid via charging stations which are either located in the home, in public places, or on privately owned commercial property. The onboard charger converts single phase mains power to DC for storage in the battery and controls the amount of power sent to the battery, preventing overheating of both the battery and the supply system/charger.
Power Inverter
The inverter is the device that converts high-voltage, high-current DC power from an electric vehicle’s batteries into AC electricity for the motor. The output is a “square wave” in its most basic form and is better suited to AC motors which contain the magnetic fields inside that need time to increase and decrease in strength.
Manufacturers of vehicle inverters are always striving to enhance their products’ design and efficiency. Recently, the practice of integrating an inverter with a motor or converter has received a lot of attention from manufacturers. For example, a motor with an integrated inverter or a single power module that combines inverter and DC-DC converter functionality offers better efficiency while reducing vehicle space and weight.
Electric Motor
EV motors function by attaching one pair of magnets or electromagnets to a shaft (i.e. the rotor) and another set to the housing that surrounds it (i.e the stator). Alternating electricity is required for motors to rotate, otherwise, the electromagnetic force would simply lock their north and south poles together. The EV motor leverages these attracting and repelling forces to rotate the shaft, converting electricity into torque and eventually turning the wheels by periodically reversing the polarity of one set of electromagnets. These magnetic/electromagnetic forces are also able to convert motion back into electricity, as in regenerative braking.
Battery Management System (BMS)
The term “Battery Management System” refers to an electrical system that regulates a rechargeable battery to ensure that it functions effectively and safely (BMS). It is essentially the brain of the vehicle and is designed to keep track of the characteristics associated with the battery pack and its cells. It then uses this information to reduce safety concerns and improve battery performance. Every model of vehicle will have a unique BMS.
Future development of EV
The growth in EVs and hybrid electric vehicles (HEVs) is climbing and by 2025, EVs and HEVs will account for an estimated 30% of all vehicle sales. This most certainly requires a nation-wide charging infrastructure and continued research and development with the expressed aim to eliminate tailpipe emissions from light-duty vehicles in the U.S. by 2035 and ideally achieve carbon neutrality in global products and operations by 2040.
According to a McKinsey report from 2021 , yearly demand for power to charge EVs would rise from 11 billion kilowatt-hours (kWh) to 230 billion kWh in 2030 as the number of EVs on the road grows. The 2030 demand projection is equivalent to around 5% of current total power consumption of just the United States. Approximately 30 million chargers would be required to supply that much power in a single year. While the majority of these chargers would be put in homes, 1.2 million would be public chargers, which would be deployed at on-the-go venues and areas where vehicles are parked for extended periods of time. The cost of hardware, design, and installation for this amount of public charging infrastructure is estimated to be in the millions of dollars. As with most of the other technologies we all use on a day-to-day basis, they are heavily dependent on a network to facilitate their usability.
Advanced battery technologies
Starting 2012, battery prices started to drop by 50% over four years making EVs more attractive. It is not only the price but also technological breakthroughs that have recently started to make EVs even more attractive.
A lithium-ion battery has a liquid electrolyte, but a solid-state battery, as the name implies, has a solid electrolyte. The advantages of solid-state batteries are that they are lighter, have a higher energy density, have a longer range, and recharge faster as a result of this.
GM and Honda have made a statement that they are sharing technology, design, and manufacturing strategies to deliver affordable and desirable EVs on a global scale. GM is already striving to advance new technologies such as lithium-metal, silicon, and the same solid-state batteries, as well as manufacturing methods that can be utilized to swiftly upgrade and update battery cell manufacturing processes while Honda is further developing all-solid-state battery technology, which it sees as a critical component of electric vehicles in the future.
Improved efficiency of electric traction motors
High-volume manufacturers have been wary of using permanent-magnet motors because of reliance on heavy rare-earth elements of which China holds anywhere from 35-40% of the world’s reserves.
Progress in the development of solid-state batteries, already discussed, is certainly one trend that will ensure the efficiency of the EVs coming out in the next few years is much better than what is available now, but there are improvements being made all along the drivetrain.
Integrated Power Modules
The power semiconductor modules used in inverters are responsible for electric power transfer between the source and load. The efficiency of such systems has improved because of advances in WBG-based devices such as SiC, MOSFETs and HEMTs. This improved efficiency, which is roughly three times that of silicon, is due to a larger bandgap,i.e., the energy necessary to make an electron accessible to conduct electricity. For example, a SiC device can withstand an electric field nearly 10 times that of silicon before failing, allowing SiC devices to function at significantly higher voltages than comparable silicon structures.
DC-Link capacitors
The term “DC link” is used to describe the point where two power conversion stages meet and an energy storage device (i.e. the capacitor) serves as a buffer for each, smoothing out the pulses and reducing the amount of peak-to-peak ripple. There are several types of capacitors that can be used in EV traction applications and they can be divided into two primary groups: electrostatic and electrolytic capacitors.
Although the electrolytic capacitors are the most popular choice for conventional motor drive applications, their short lifespan, limited current conduction capability, and low-frequency operation make them not suitable for use as DC-link capacitors in EV inverters.
In contrast, electrostatic capacitors have non-polar construction in which plastic films and ceramic are used as dielectrics. Capacitors with a plastic film dielectric (particularly polypropylene) have a very low equivalent series resistance (ESR) due to the fact that current does not have to flow through an electrolyte. Electrostatic capacitors can be produced in very high voltages and can be used both in AC and DC circuits.
We are always striving to stay abreast with trends in the EV market and invite you to check out the sourcing options available at TECHDesign. Let our team of specialists assist you in finding the ideal solution for your needs.